Product Description
Vacuum Tray Dryer is suitable for the rapid drying of thermal sensitive materials easily resolved, polymerized, or deteriorated under higher temperatures. Sterilization can be conducted prior to the drying process, during which no matter is allowed to enter the product. Static vacuum dryer eliminates the configuration damage of the drying materials therefore widely used in pharmaceutical, chemicals and foodstuff, etc.
Principally, drying under vacuum is environmentally friendly because the Evaporated Solvents can easily be re-condensed. These solvents can then either be recycled or disposed of without any problem.
Drying of solvents in Ex-proof ovens may solve the safety problem in the oven but not the environmental aspect. The solvent vapor is blown out of the oven through the exhaust system Furthermore, there is a risk of uncontrolled mixture formation.
Tray Dryer Working Principle:
- In-tray dryer, hot air is continuously circulated. Forced convection heating takes place to remove moister from the solids placed in trays.
- Simultaneously the moist air is removed partially.
- Wet solid is loaded into the trays. Trays are placed in the chamber.
- Fresh air is introduced through the inlet, which passes through the heaters and gets heated up.
- The hot air is circulated by means of fans at 2 to 5 meters per second.
- Turbulent flow lowers the partial vapor pressure in the atmosphere and also reduces the thickness of the air boundary layer.
- The water is picked up by the air. As the water evaporates from the surface, the water diffuses from the interior of the solids by the capillary action.
- These events occur in a single pass of air. The time of contact is short and the amount of water picked up in a single pass is small.
- Therefore, the discharged air to the tune of 80 to 90 % is circulated back through the fans. Only 10 to 20% of fresh air is introduced.
- Moist air is discharged through the outlet. Thus, constant temperature and uniform airflow over the materials can be maintained for achieving uniform drying.
- In the case of the wet granules as in tablets and capsules drying is continued until the desired moister content is obtained.
- At the end of the drying trays or trucks are pulled out of the chamber and taken to a tray dumping station.

Special Features:
- The main body and door are made in SS 316 with a rigid flange.
- Shelves (hollow type) in SS 316 with baffles
- Trays (without back folding) in SS 316
- Condenser (shell & tube) and Receiver in SS 304 for solvent recovery
- Digital Temperature Indicator (FLP) at H.W. Inlet and Outlet
- Digital Temperature Indicator (FLP) at vacuum line
- Dial type vacuum gauge in the vacuum line
- Dial type Temperature gauge in body
- Glass view provided on door and receiver
- Flow glass provided to monitor condensation between condenser and receiver
- Validation port
- Provision for Nitrogen purging
- Vacuum brake valve provided in the vacuum line
- Construction and finish as per cGMP standard

Additional:
- Condenser and receiver are made in SS 316
- 300 mm wide SS 304 skirting all along the flange
- 50 mm thick glass wool insulation on the vacuum chamber outer surface except for the door. The insulation is enclosed and covered with a removable SS 304 angle frame
- Digital temperature controller with pneumatic operated valve at hot water/steam inlet
- 2 stage water ring type vacuum pumps (partial SS) run by FLP motor
- Hot water system with circulation pump
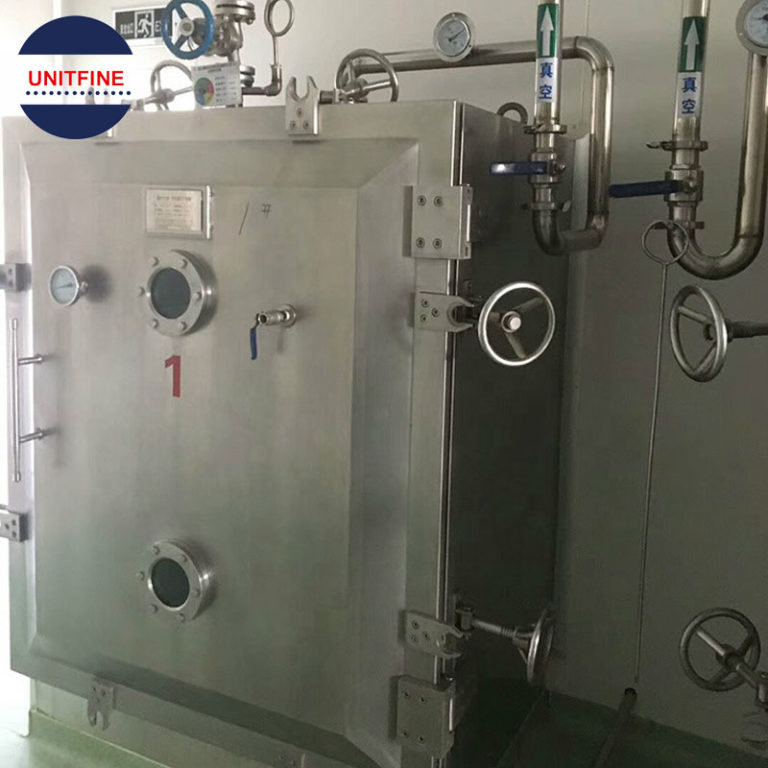
Applications:
- Chemicals
- Dyestuff
- Pharmaceutical
- Food Products
- Colors
- Nutraceutical
Testing Parameters:
- The vacuum dryer shelves are hydro-tested 5 kg/cm2 assembled condition. The vacuum chamber is tested for leaks under vacuum.
Capacity:
- Standard models range from 3 trays to 96 trays
Model Available
Models available
Model |
YZG-600 |
YZG-1000 |
YZG-1400A |
FZG-8 |
FZG-15 |
FZG-30 |
FZG-38 |
Inner Size of Drying Oven (mm) |
600 × 976 |
1000 × 1527 |
1400 × 2054 |
730 ×1200 ×1450 |
1500 ×1400 × 1220 |
2200 ×1500 × 1500 |
2200 ×1500 × 1600 |
Overall Size Of Drying Oven (mm) |
1135 × 810 ×1020 |
1693 × 1190 ×1500 |
2386 × 1675× 1920 |
930 ×1380 ×1540 |
1513 ×1924 × 2060 |
2400 ×1680 × 2050 |
2400 ×1680 × 2250 |
Layers of Drying Rack |
4 |
6 |
8 |
8 |
8 |
8 |
10 |
layer Distance (mm) |
81 |
102 |
102 |
122 |
122 |
122 |
122 |
Size of Tray (mm) |
310 × 600 ×45 |
250 × 410 × 45 |
400 × 600 ×45 |
460 × 640× 45 |
460 × 640 ×45 |
460 × 640 ×45 |
460 × 640 ×45 |
Drying Tray Number |
4 |
12 |
32 |
16 |
32 |
64 |
80 |
Pressure of Drying Rack Tube (Mpa) |
≤ 0.784 |
Temperature of Drying Rack (ºC) |
-35 to 150 |
No-load Vacuum degree within the tank (Mpa) |
-0.09 to -0.096 |
Weight of drying oven (kg) |
250 |
800 |
1400 |
1680 |
2100 |
2850 |
3200 |
Recommended products for You
-
UFC Continuous Automatic Electric Heating Roaster