Product Introduction
Colter type mixer can handle the mixture of solid powder and aggregates, it adapts to the batch mixing process which adding liquids, it is widely used in the food industry, chemical industry, and building industry, it is particularly used in food additives, ready-mixed mortar, composting technology, sludge treatment, rubber plastic, special building materials industry, strong cutting action makes it have a mixture quality with high performance.
Performance introduction:
1. Flexible selection scheme : The mixer can adopt carbon steel, manganese steel, 304 stainless steel, 316L stainless steel, 321 stainless steel and other steel materials, and different material can also be used in combination; The equipment material selection is divided into: contact with the material and non-contact with the material; The internal mixer can also add the coating or protective cover which has the functions of anticorrosion, anti-cohesion, isolation, wear resistance; Stainless steel surface treatment is divided into sand blasting, wire drawing, polishing, mirror surface processing, etc., and can also be applied to different using parts to use;
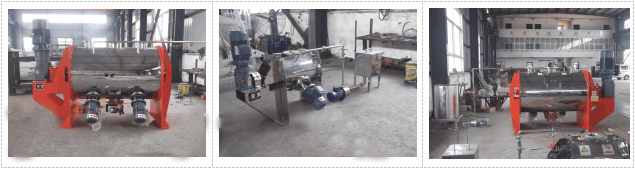
2. Reliable drive configuration : The drive device in different ability, different power, and different output speed will be equipped on the mixer according to the material properties, startup mode, and the stirring method.
Driven motor selections are: general motors, explosion-proof motor, variable frequency motor, high efficiency and energy saving motor, high protection grade motor, and the motor under different voltage; Commonly used reducer: R, K, F series gear reducer, cycloidal pin gear speed reducer, general type gear reducer, planetary gear reducer; Commonly used connection mode: directly connected-type, pulley connection, hydraulic coupler.
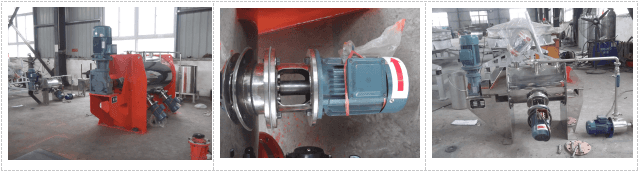
3. High efficient mixing device : Plough type cutting head of Colter mixer is detachable, can achieve the result of rapid replacement; After the wear-resistant treatment for the colter, it is more adapted to the wear faster conditions.
Different stirrers can be configured according to different material properties.
Main shaft stirrer: general colter type, saw-toothed colter, scraper razor; High-speed shear fly knife: multiple-plate cross knife, double lotus leaf blade;
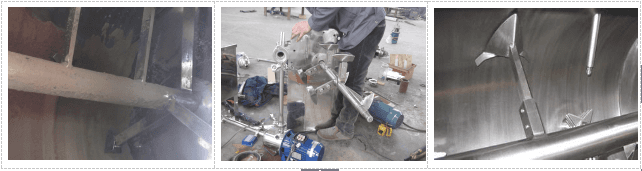
4. Excellent feeding device: Colter type mixer generally configurate pneumatic surface flap valve, when the valve is closed, the valve surface flap properly fit cylinder cambered surface, in the mixing process, no redundant stir dead angle, make the mixing material more evenly. The driving types of valve can be manual, pneumatic, and electric.
The referenced valve also has powder ball valve, cylinder valve, the plum blossom dislocation valve, powder butterfly-valve, rotating feed valve, etc.
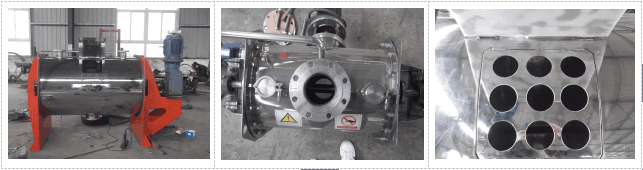
5. Powerful auxiliary components : Mixer can be mounted a variety of components, commonly, it has coil steam jacket, cellular pressure jacket, circulating medium jacket, on-line sampling valve, high-speed knife throwing, temperature detection, weighing system, dust purification and other components. Different mixer jacket is adopted according to different heat medium, it may be heating or cooling, the highest temperature is within 250 degrees Celsius.
When adding a small amount of liquid, the hydrojet and spray device need to be equipped, it is more advantageous for the liquid dispersed and mixed evenly into the main ingredient.
Spray system consists of three basic module: pressure source, liquid storage tank and sprayer.
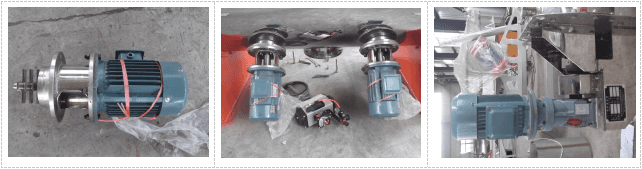
6. Rigorous shaft seal : Three kinds of sealing mode are designed for mixing machine: packing seal, combined gas seal, mechanical seal; To solve the main shaft seal of granular, powder, micron grade powder, liquid, and slurry states.
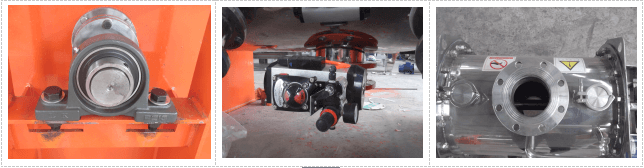
Working Principle:
Total equipment volume: 0.3 ~ 30m³
Processing capacity for each batch : 0.1 ~ 20 m³
Processed materials for each batch:0.3~15t
The mixing time: 3 ~ 15 minutes
Drive configuration power: 3 KW – 160 KW
Equipment materials: 316L, 321, 304, carbon steel
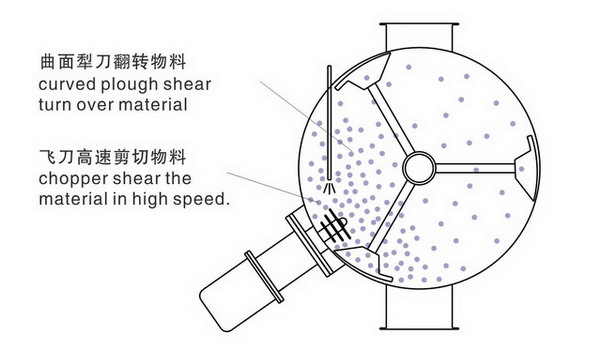
Colter type mixer is for single shaft type forced mixing equipment, multi groups of colter stirrers are installed on the main shaft, and malposed continuous installating, it avoids stirring dead corner on the structure, when it is running, continuous type spiral centrifugal force are produced, the malposed colter continues stirring, spiral centrifugal material flow constantly overlap, strike, and make the material boiling, it forms convective circulation, mixing material rapidly.
The cluster materials such as fiber, the powder which is the cluster affected with damp and adding liquid condensed powder, through the high-speed fly knife installed in the colter mixer, when mixing materials, combined with the colter stirrer, form the convective circulation, then the materials will be scattered and separated.
High-speed fly knife is installed under the colter mixer drum lateral direction of 45 degrees angle, cutting head into cylinder, when mixing, materials are driven to the fly knife range by the colter, sheared by the high speed.
Selection and parameters:

è§„æ ¼åž‹å·
Specification |
UDH-0.3 |
UDH-0.5 |
UDH-1 |
UDH-2 |
UDH-3 |
UDH-4 |
UDH-6 |
UDH-8 |
UDH-10 |
UDH-15 |
有效容积(m³)
Working capacity |
0.18 |
0.3 |
0.6 |
1.2 |
1.8 |
2.4 |
3.6 |
4.8 |
6 |
9 |
批次最大产é‡ï¼ˆkg)
Max.Working capacity for each batch |
200 |
300 |
600 |
1200 |
1800 |
2500 |
3600 |
5000 |
6000 |
9000 |
转速(r/min)
Rotate speed (rpm) |
130 |
130 |
85 |
63 |
63 |
42 |
42 |
33 |
33 |
28 |
驱动功率kw
Driven power |
5.5 |
7.5 |
11 |
15 |
22 |
30 |
45 |
55 |
75 |
90 |
设备é‡é‡ï¼ˆkg)
Weight |
550 |
800 |
1000 |
1800 |
2500 |
3500 |
4200 |
4800 |
5800 |
7000 |
L |
2200 |
2700 |
3200 |
4100 |
4350 |
4700 |
5400 |
6500 |
5600 |
6000 |
C |
900 |
980 |
1000 |
1250 |
1450 |
1500 |
1700 |
2200 |
2500 |
2800 |
H |
900 |
1200 |
1350 |
1600 |
1800 |
1950 |
2300 |
2600 |
2900 |
3000 |
Selection methods:
- Ensure the material volume is in the range of 0.1 to 20 m for each batch mixing, and select the equipment in corresponding specifications.
- Select equipment material, material is divided into: contact with the material parts, non-contact with the material, the other equipment parts keep original material.
(Material is selected according to the factors of material properties, working condition requirements, and health level. Regularly, it has carbon steel, 304/316L/321 stainless steel)
(Surface treatment will be ensured according to the requirement after selecting the material)
- The drive ability of configuration will be ensured according to the proportion of material, liquidity, etc, as well as the starting standard.(The starting standard is divided into: heavy start, no-load start).
- On the basis of the actual process, adding the auxiliary function components, such as spray, heating/cooling, etc.
- Design equipment’s opening mouth, such as feeding mouth, clearing mouth, exhaust hole, etc.
- Select discharging mode and drive mode, it is divided into manual, pneumatic, and electric.
Important note: Equipment selection is the important link, the detailed material information and process arrangement should be provided as far as possible, so that our company’s professional staff can provide you with high quality technical services.
Combination scheme:
Configuration 1: use the ton bag raw material, crane lifting, combine dirt catcher for feeding directly;
Configuration 2: set up multiple platform, artificial feeding, adopt ton packaging machine after mixing discharging;
Configuration 3 : Use the most simple and easy mixing equipment, feeding and charging directly , configurate forklift for loading and unloading;
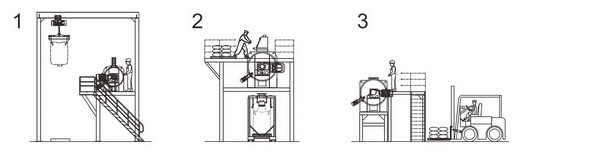
Configuration 4: use artificial feeding platform, after mixing, spiral lift the material into finished product storehouse, follow the packaging equipment;
Configuration 5: use vacuum feeding way, feeding on the ground, dopt ton packaging machine after mixing discharging;
Configuration 6: multi-stage vacuum feeding conveyor, after mixing storage, package again;

Configuration 7: multi-layer working station design, elevator feeding, integrated tower structure for feeding, warehousing, mixing, storage, packaging;
Configuration 8: use bucket elevator for feeding, feed into the mix, storage, packaging;
Configuration 9: the up and down integrated structure for vacuum feeder feeding, mixing, warehousing and packaging;
Configure 10: the up and down integrated structure for artificial feeding, mixing, warehousing, and packaging;
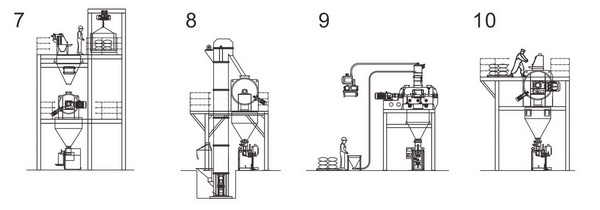